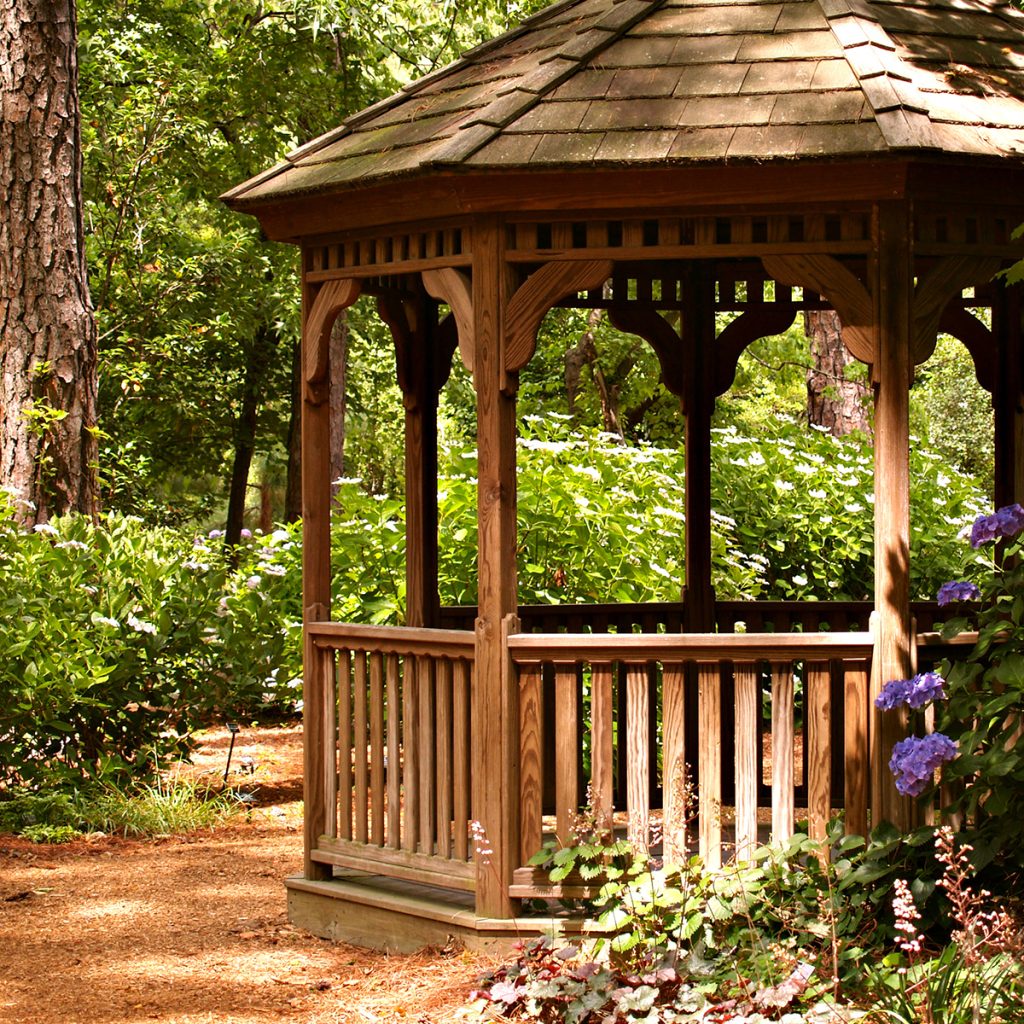
The Science Behind Pressure-Treated Wood
How Specialized Treatments and Processes Enhance Durability and Longevity
Have you ever wondered what makes wooded structures stand strong against rain, insects, and rot? The solution lies in pressure-treated wood. The pressure treatment process is critical to expand the lifespan of natural wood (making it applicable for construction projects), reducing the demand for new timber, and minimizing waste.
However, matching a pressure-treated wood type to the project’s unique needs includes considering factors such as potential moisture exposure, structural demands, and even aesthetic preferences. And the specific pressure treatment processes and preservatives selected will depend on the wood’s end use and application. Ultimately, the wood used in the construction of decks, piers, fences, and infrastructure does not simply go from forest to finished project. It first undergoes a carefully engineered, scientific process to meet the demands of its intended purpose.
Understanding Key Preservatives Used in Pressure-Treated Wood
There are three main preservatives that are used to extend the lifespan and durability of wood by protecting it from moisture, decay, insects, and other environmental factors. Each possesses unique properties that makes it suitable for varying applications.
- Chromated Copper Arsenate (CCA) – CCA wood preservative systems have stood the test of time, having been used since the 1940s. CCA is a group of pesticides containing chromium, copper, and/or arsenic that protect the wood against termites, which can degrade the quality of wood products. While CCA is no longer used in the construction of decks, fences, walls, or other residential applications, it is still used for utility poles, foundation piling, permanent wood foundations, and other industrial and marine applications.
- Micronized Copper Azole (MCA) – MCA is a water-based wood preservative that contains micronized copper particles and other chemicals. MCA is less harsh than earlier versions of pressure treatments and is often used for interior and exterior above ground, ground contact, and fresh water immersion applications. Culpeper uses MicroPro® technology, a revolutionary way to pressure treat wood for decks, fences, landscaping, and general construction uses for enhanced corrosion performance and building code compliance.
- Borate – Borate is a chemical compound made up of borate salts dissolved in water, which are commonly used to protect wood from decay, fungi, and insects such as carpenter ants and termites. In fact, Culpeper’s ADVANCE GUARD® Borate treatment is recognized by the industry-standard blue tint. The addition of blue dye during the treatment process makes it easy for building inspectors to identify that the lumber is borate treated. These materials are often used in construction for sill plates, trusses, beams, blocking, joists, studs, and rafters.
Locking It In: Culpeper’s Treatment Process
Manufacturers select the preservative based on the wood’s intended use, but the treatment process is just as important as the preservatives used. This procedure locks the chemicals into the wood fibers for long-term performance.
Before treatment, Culpeper stores the lumber in dry conditions to enhance its appearance and prevent any premature decay. Each load of lumber is inspected for moisture content, grade, and appearance.
Pressure treatment is a carefully controlled process of pressure and vacuum cycles within an enclosed cylinder. The process forces preservatives deep into the cellular structure of the wood, forming a chemical bond that, in the final wood product, resists decay and attack by insects. This bonding process, known as “fixation,” locks the preservative into the wood, making it highly resistant to leaching or dissolving.
After treatment, the Culpeper team analyzes samples in its quality control laboratory to ensure they meet the standards of the American Wood Protection Association and the International Code Council. Pressure-treated lumber is then drained on a drip pad and stored under a roof or kiln dried.
The result: Pressure-treated lumber engineered for lasting performance and durability in every application.
Protection That Lasts: Guarding Against Insects, Rot, and Moisture
Since pressure-treated wood withstands both biological and environmental stressors, it lasts longer without the need for frequent maintenance. Pressure treatment chemicals are toxic to wood-damaging organisms and fungi, which prevents the wood from rot, mold, and termite infestations. By deeply embedding these chemicals during the treatment process, the wood adopts a protective barrier that does not just sit on the surface but permeates its entire structure.
Moisture is the primary cause of wood decay, leading to warping, splitting, and ultimately weakening the wood. The chemicals used in pressure-treated wood significantly minimize or eliminate the wood’s ability to absorb water, allowing it to withstand wet environments without the typical consequences that an untreated piece of wood would face. This resistance to moisture keeps the wood from breaking down and maintains its structural integrity over time.
Pressure-treated wood offers long-term durability in high-moisture or high-contact areas where an untreated alternative would quickly decay. From garden beds and outdoor walkways to docks and retaining walls, it provides a strong, sustainable solution for the most demanding applications.
Built to Last: The Enhancements of Pressure Treated Wood
Pressure-treated wood is more than just a practical building material. It is a testament to the power of science and innovation in construction. By harnessing advanced chemical formulations and precision-engineered treatment processes, manufacturers of pressure-treated wood produce a product that achieves unparalleled durability and resilience for a natural material. Whether it is needed to fend off termites, moisture, rot, or other harsh environmental conditions, pressure-treated wood remains critical in building long-lasting, sustainable structures.